


Next, subtract 1 from that answer: 5 – 1 = 4.
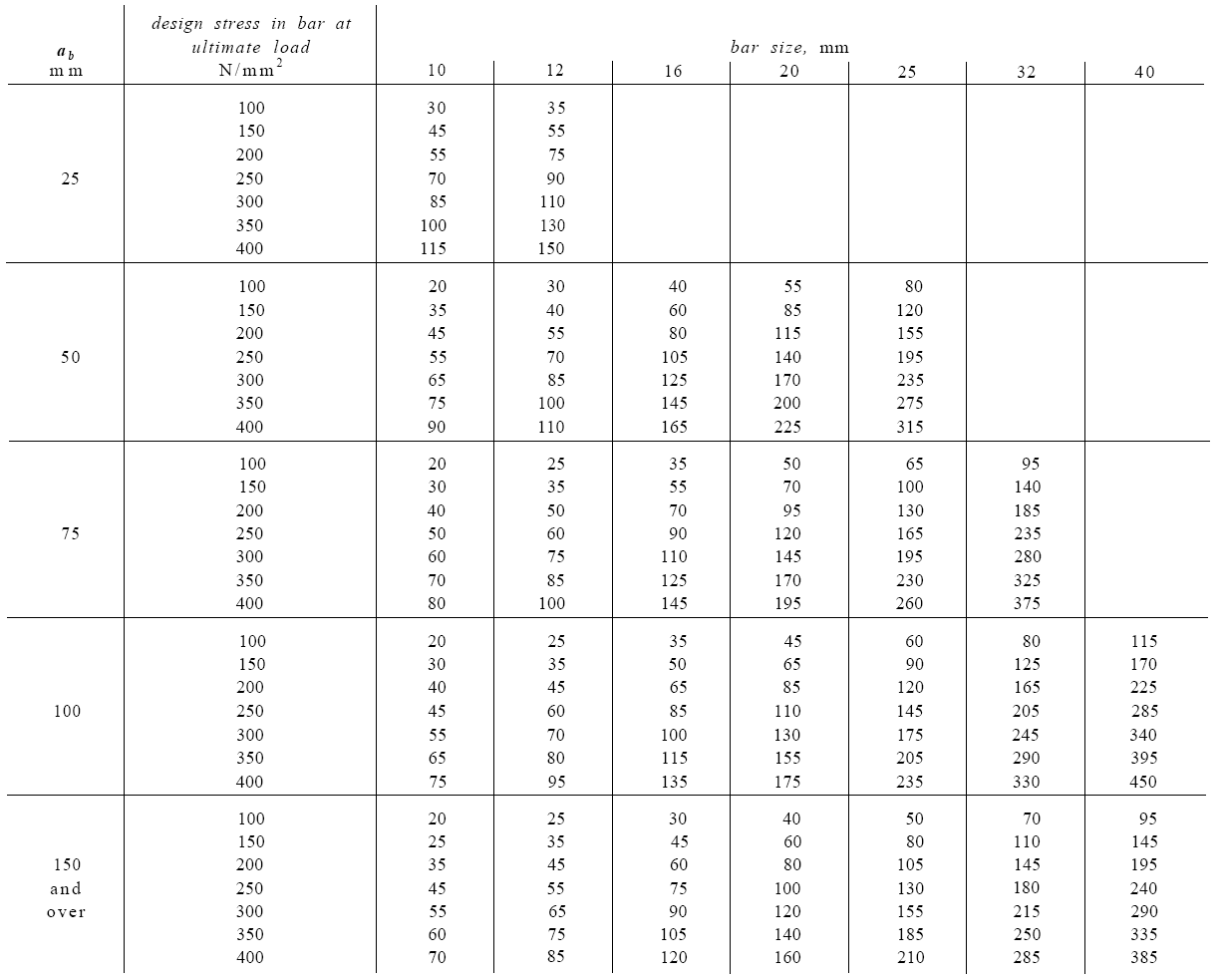
To state your example, “If the steel has a tensile reduction value of 10 percent, divide 50 by that value: 50/10 = 5.

You described a rough rule to find a steel’s minimum bend radius: Divide 50 by the material’s reduction percentage, as specified by the material supplier, subtract by 1, and then multiply by the plate thickness. Q: In a previous Bending Basics article, you mention a “material’s tensile reduction percentage” used for calculating the minimum inside bend radius of various metals. Grain, increases the required minimum inside radius of If the tube is longer and cannot be cut, this incorrect calculation of the laser cutting position has resulted in irreparable damage to the entire tube processing procedure.Longitudinal bending, or bending with the material Calculating the laser cutting position incorrectly means that the resulting bent tube will be longer or shorter than it should have been. The value for the length of the tube bend is also important for determining the exact point at which the laser cut needs to be made, as well as the length of this cut. This value will vary depending on tube diameter and wall thickness, as well as the average bend radius and alloy percentages.Ī Ø30 x 2 mm steel tube with the same radius as a Ø30 x 2 mm aluminium tube will nonetheless have a different coefficient. To calculate the exact length of the bend, the product of the above formula must therefore be divided by another coefficient – known as the coefficient of elongation. This elongation can have the following consequences: To verify the feasibility of bending round steel tubes, the ratio between the average bending radius, diameter and thickness of the tube concerned is considered. In this case, tests must be run in order to evaluate whether the K-factor can be reduced and if special bending jigs need to be constructed. K 0.08 > K > 0.05 – Tube bending is possible only when using a movable, internal mandrel in conjunction with a wiper die.0.10 > K > 0.08 – A fixed bending mandrel with a wiper die – a special tool to restrict tube deformation – will be needed for bending the tube.0.30 > K > 0.10 – The bending process is of normal difficulty: using only an internal, fixed bending mandrel will be sufficient.K > 0.30 – Bending the tube is more ‘straightforward’ and there is now need to use special support jigs that would need to be manufactured ad hoc.The difficulty of the tube bend is inversely proportional to its value: the difficulty increases with a low K-factor and decreases with a high K-factor. This formula produces the value for the K-factor.
